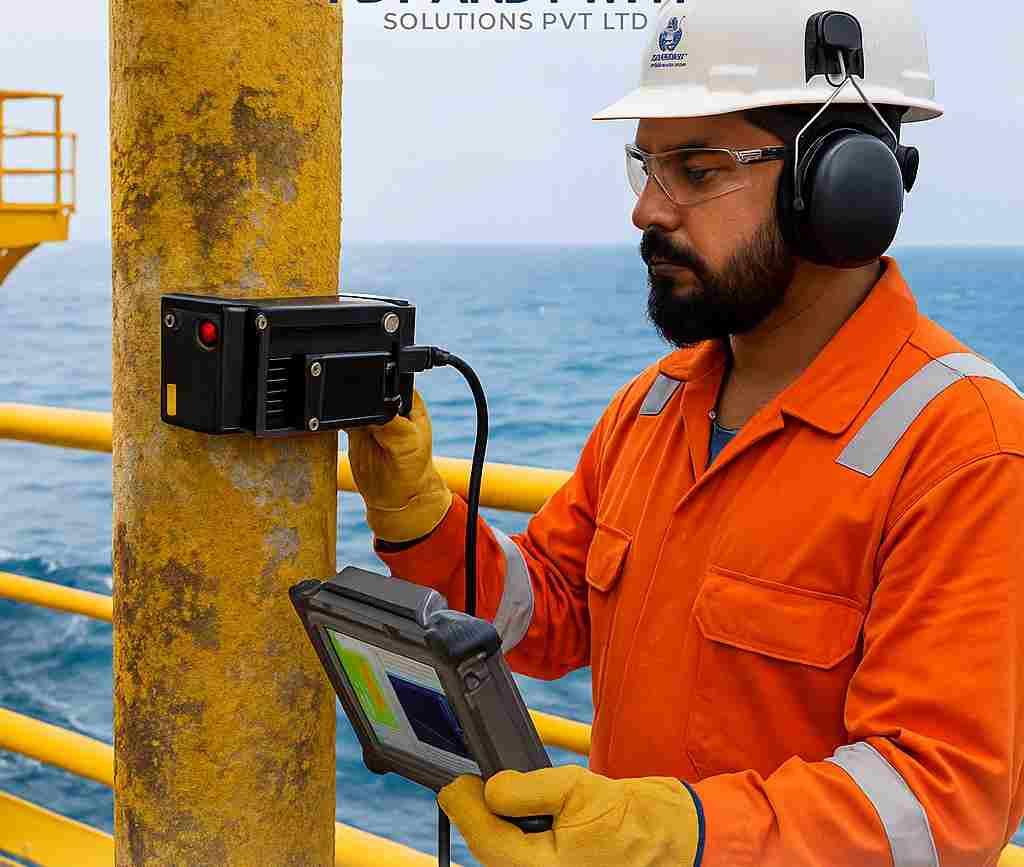
Pulse Eddy Current (PEC) is an advanced electromagnetic inspection technique used for non-intrusive detection of corrosion and wall loss in metallic structures — especially those covered by insulation, coatings, fireproofing, or marine growth. PEC has revolutionized asset integrity management by allowing fast, safe, and cost-effective inspection without surface preparation or removal of protective layers.
How Pulse Eddy Current Technology Works?
PEC works on the principle of electromagnetic induction. A coil emits a short-duration electromagnetic pulse, generating eddy currents in the conductive material (typically carbon steel). These eddy currents diffuse through the metal and decay over time.
A receiver coil measures the decay rate of these eddy currents, which correlates with the thickness of the material. The decay becomes faster when the metal is thinner due to corrosion or erosion. This allows the PEC system to estimate wall thickness through multiple layers — including insulation, cladding, coatings, or fireproofing — with no need for contact or surface access.
Key Applications of PEC Technology:
PEC is widely used in industries where insulation, coatings, or difficult access restrict traditional inspection techniques. Its most common applications include:
Corrosion Under Insulation (CUI)
Storage Tank Floor Mapping
Risers & Splash Zone Inspection
Subsea & Underwater Pipeline Assessment
Pipe Supports & Touch Points
Fireproofed Steel Structures
Pressure Vessels and Columns
Heat Exchanger Shells & Large-Diameter Tubes
FPSOs, Offshore Platforms & Wind Turbines
District Heating, Cleanrooms & Utility Pipelines
Advantages of PEC Technology:
Non-Intrusive & No Surface Prep
Inspects through insulation, coatings, fireproofing, or marine growth — no removal needed.
Safe and Efficient
Reduces confined space entry, hot work, and scaffolding — enhancing safety and minimizing downtime.
Wall Loss Mapping
Provides wall thickness estimation for identifying generalized and localized corrosion.
Data Logging & Repeatability
Enables trend monitoring over time for RBI (Risk-Based Inspection) strategies.
Versatile Deployment
Can be used manually, semi-automated, or mounted on robots, drones, crawlers, or ROVs.
Ideal for In-Service Assets
Inspections can be done during operation, avoiding shutdowns and production loss.
PEC vs Other Technologies
Technology Coating Penetration Wall Thickness Estimation Flaw Sizing Contact Required:
PEC ✅ Excellent ✅ Good ❌ Limited ❌ No
UT ❌ Poor ✅ Excellent ✅ Excellent ✅ Yes
RT ✅ Good ✅ Good ✅ Moderate ❌ No
MFL❌ Poor ✅ Moderate ✅ Moderate ✅ Yes
Future Scope of PEC:
The evolution of PEC is ongoing. Pulse Eddy Current Array (PECA), advanced software analytics, robotic integration, and AI-driven data interpretation are pushing the boundaries of what PEC can deliver. Expect:
Improved spatial resolution
Multi-probe array configurations for faster coverage
Cloud-connected PEC data logging for digital twins
Enhanced performance in complex geometries
Pulse Eddy Current Technology is a vital inspection tool for industries managing insulated, coated, or hard-to-access steel assets. It is not a replacement for every NDT technique but a powerful complement to existing methods, especially in situations where traditional inspection is not feasible.
Whether for Corrosion Under Insulation (CUI), splash zones, or subsea assets, PEC delivers high-value insights, enabling safe, predictive, and cost-effective maintenance planning.